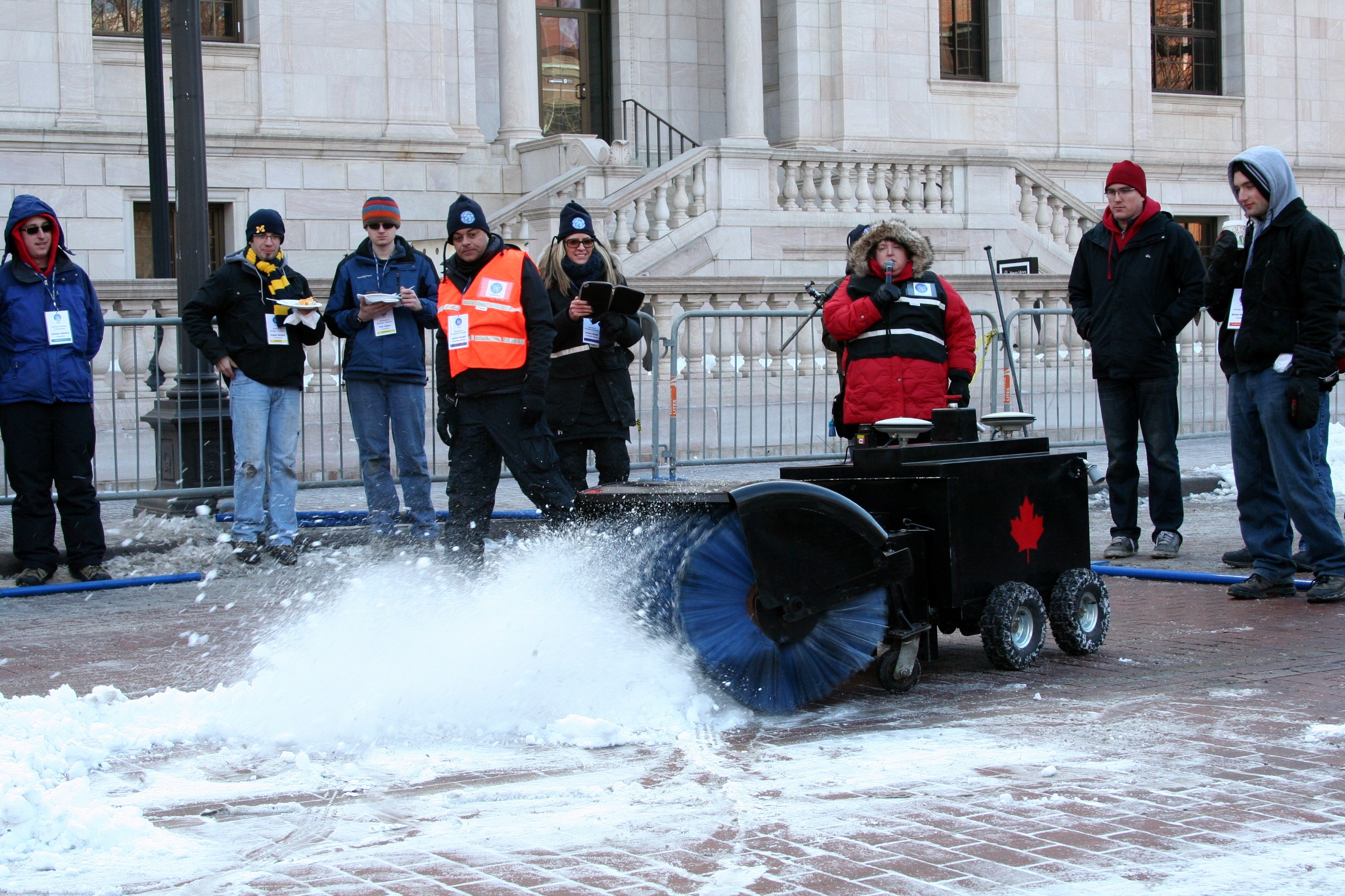
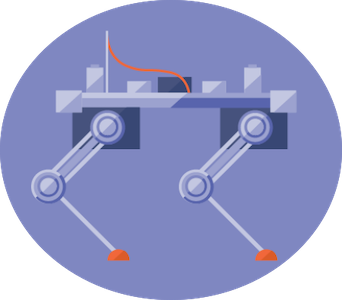
In a small park, a little way off the central drag of the St. Paul Winter Carnival in Minnesota, a group of people have gathered to watch a small robot laboriously shoveling snow into a box. The robot’s creators are looking nervously on as it scans its surroundings to try and work out how best to clear the area rapidly, accurately and safely.
This is the fifth annual Autonomous Snowplow Competition held by the Institute of Navigation. Teams from around the United States compete to build what are essentially snow-clearing Roombas–robots that can autonomously remove snow from an area of ground. Vacuum-cleaner and lawnmower robots of this type have been with us now for more than 10 years, but an autonomous robotic snowplow remains frustratingly out of reach, mostly because of the far tougher conditions it has to operate in.
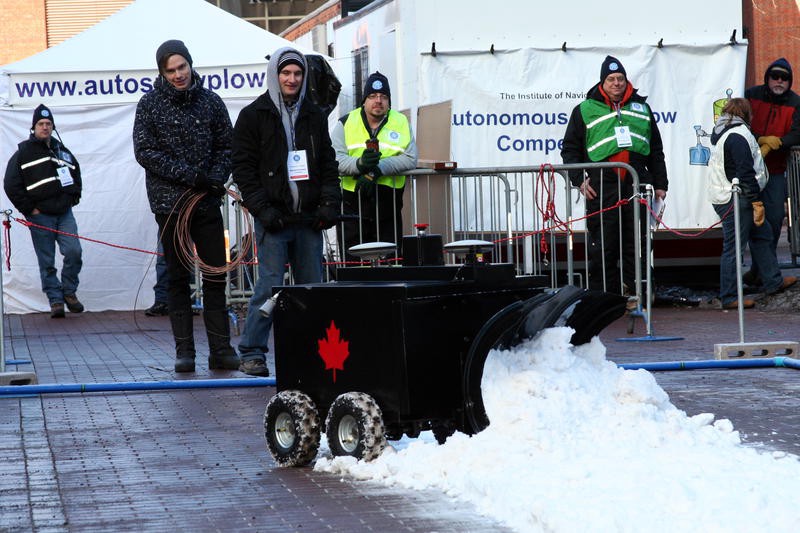
During the competition, the robots are tested over the course of three days. The teams first present their designs to judges, then compete twice in live events the public attends. It’s a high-pressure situation, and things frequently break. “Many of the student teams are testing in their laboratory on linoleum or tiled surfaces, and everything seems to work well at 70 degrees F,” said Dr. Suneel Sheikh the CEO and chief scientist at Aster Labs, who helps run the competition every year. “But as soon as we get down to 0 degrees F with [the] possibly [of] some snow or moisture and exposed electronics, things stop working.”
It’s the second competition that the institute has run. The first, for robotic lawnmowers, lasted for nine years from the mid-90s and culminated in significant development of the hardware and navigation tool sets that make these types of vehicles commercially viable today. Sheikh hopes to do the same thing for snowplows and was happy to see many of the lawnmower competitors enter in the first year. “They literally just took off the grass clipping hardware and put on a snowblade, then used their instruments to do the competition,” he said.
That didn’t work too well, and it’s taken time for the teams to adjust to the challenges of a snowy environment. The first hurdle was traction–but that’s been solved by increasing the weight of the vehicles and adding snow tires with very deep treads. Another is vision. “Teams that have tried to do image-processing have to deal with the chance that it could be snowing,” said Sheikh. This year saw several attempts to address this, with one team opting to lay magnetic strips around the boundary and use a magnetometer so the robot knows where it is in the field.
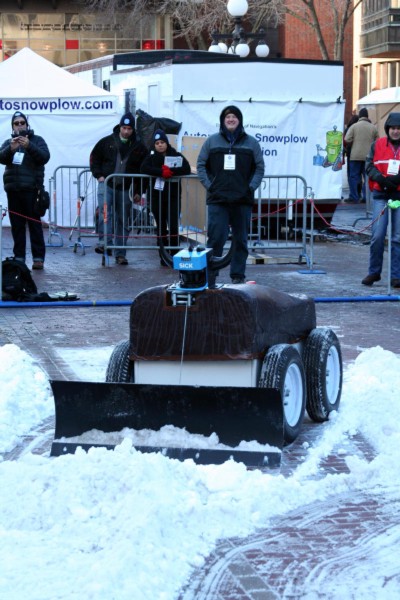
But the winning team, Zenith 2.0 from the University of Michigan, Dearborn, opted for a more economical approach than their competitors. “In the real world, no one is going to buy a $30,000 product to accomplish this task, and no one is going to buy a product that involves 30 minutes of setup and calibration,” said Benjamin Pollatz, the team captain. “So, we made a prototype that is both cost-efficient and easy to set up. The vehicle only uses a camera for all navigation.”
That’s an approach that appealed to Sheikh, whose ultimate goal is to make autonomous snowplows as affordable as a robotic lawnmower. “What I’d like to see is something we could launch as a commercial product that’s in the several-thousand dollar range instead of the multi-thousand dollar range. Something that’s economical but easy to implement in someone’s home,” he said. “I wouldn’t say we’re there yet.” But after a few more years of competition, the snowy streets of St. Paul might just become the birthplace of the next wave of robotic janitors.

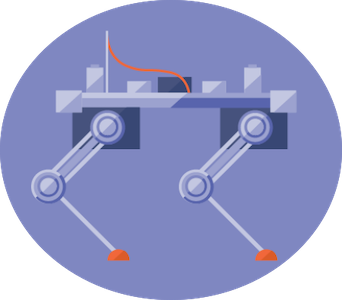
This piece is part of How We Get To Next’s Robots Vs Animals month in November 2015. Don’t looking at how chatbots will change our lives. If you liked this story, please click on the heart below to recommend it to your friends.